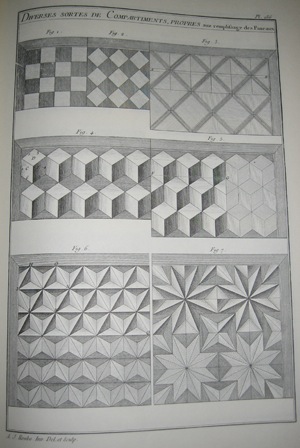 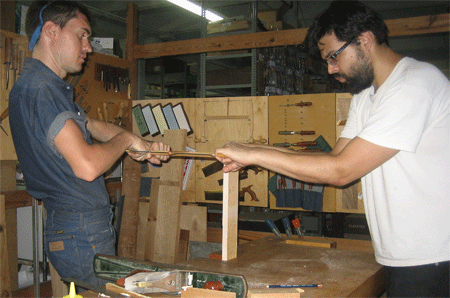 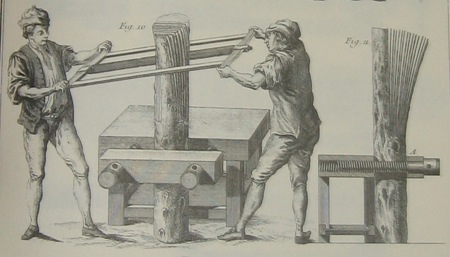 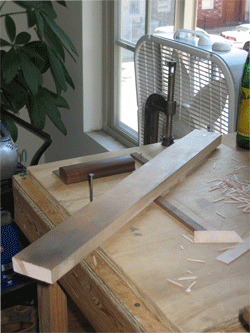 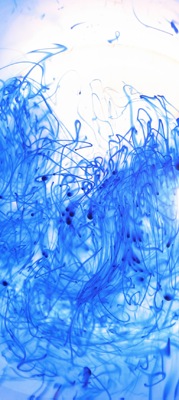
A large copy of Roubo sits high up on a shelf above my desk at Tools for Working Wood. It is a deliciously large edition with enormous detailed plates. One of my favorite groups of plates details several abstract patterns and several tools of the Eboniste. Some of the pages also include small vignettes showing little men at work. These miniature two dimensional craftsmen complete tasks in bizarre quasi-isometric perspective. In one plate they saw an entire log into a stack of veneer, in another a man wearing a jacket, vest, ruffled shirt and tights burns the edges of his veneer...
With these plates as my inspiration I decided I wanted my humidor to be covered edge to edge in a simple pattern. I chose a simple repeating parallelogram pattern (the one in the center of the Roubo plate/first photo) on the assumption that it was low lying fruit. It turns out I was wrong about the height of this tasty old French fruit (at least in relation to my skill level) but I very much like the pattern; It's figure/ground relationship is down right baroque.
I sawed a maple board into strips of veneer and then used a scraper to scrape one side of each strip smooth. Scraping took hours and a toll on my hands. In hind sight I don't know why at this point I failed to understand that I was shoving off into a sea of monotony. Once I had scraped one side of each of the strips I shuffled through them to find the thinnest one, and then found two pieces of card stock a little thinner than it. I used these on either side of the scraper as a depth stop to allow me to scrape the strips to thickness. This really took a long time, and I began to second guess my methods. The problem was that my scraping technique only got the pieces sort of close in thickness. They're all within a tolerance range of maybe +/- .010". That's very ish.
At this point I should have taken the time to make a real thickness scraper to get the strips consistent. But I didn't. This decision will surely cause problems down the line. I know it will, but honestly my aching fingers couldn't stand the thought of any more scraping.
To get consistent dimensions and angles on 450 identical parallelograms I built a fixture. It has an arm that pivots on a nail and two parallel stops (the walnut bits) to keep the veneer at the correct angle. I used two stops in order to allow me to always have the little parallelogram under the compression of the pivot arm and against the flat back of the veneer blade. Because Veneer saws have a beveled blade (except for King Kong) they cut an asymmetric kerf* in the veneer. One side of the kerf cut by the flat back of the blade is at 90 degrees to the surface. The side cut by the bevel is at about 75 degrees. Having two stops allowed me to keep the edges of my parallelograms square to their faces.
I used the 15-60 blade in my veneer saw. Even though my veneer strips were sawn (not machine sliced) after scraping they weren't thick enough to necessitate using King Kong. Of course King Kong would have cut the strips with fewer strokes of the veneer saw but in this case the difference in cutting speed was only about one stroke. I decided the burnished veneer edge left by a beveled blade was worth 900 extra strokes so I stuck with the 15-60 blade. I may have been wrong.
I took to working in shifts cutting the pieces. I would come home from work and spend an hour cutting each day. As the pile of empty beer cans and bottles on my lucky bench grew I began to imagine myself involved in a slightly sick historical re-enactment, alone and adrift at an endless labor. Like Hemmingway's old fisherman I yearned for the aid of an unpaid intern. I spent hours cutting and thinking about the wildly complicated patterns I would make... if only the boy was here! At times, the beer and Hot 97 took hold and I would pause and count my pieces...105...168...201...289...312... As each count came up short I cursed my weakness, and swore to double my resolve and/or crack a fresh brew.
Finally my parallel maple boat came to shore with 450 gloriously identical parallelograms. Surely Girlfriend would swoon whilst Brooklyn burst into song at my accomplishment...
"Girlfriend!! look how many little pieces of wood I've made! They're identical!"
"HmmmMMMMMmmmmm"
With my 450 identical bits of wood I did a few maths to approximate how many of each color would be needed. Then I pulled out the Devil Spring Vodka and mixed up 4 batches of Lockwood dye. I dunked/soaked the pieces and set them to dry on artfully crumpled tinfoil to allow air flow on all sides. Once the pieces were dry I piled them together and looked around for some sand to burn the edges. Unfortunately our supply of household sand had been used by an ungrateful hermit crab now panhandling his way down the Bowery.
I decided salt would do just as well...
I poured the salt into a small cast iron pan and heated it on low. I burned two edges on each piece of dyed veneer. I got good enough to where I could place enough pieces in the pan at once that after placing the last one, the first would be ready for flipping. The process went swimmingly and smelled like bacon fat, and maple. I managed to get quite a consistent burn on both the wood and my forearm.
In hindsight, I should have started with a sheet of machine cut veneer. It remains to be seen what consequences the uneven thickness of my pieces will have. It is my hope that by their careful arrangement I can minimize their thickness differences enough to keep from scraping through the dye while leveling them on the box. If not, well, I can't imagine letting a little thing like screwing up stop me now.
*Addendum*
Does a beveled veneer blade cut a kerf? This is the subject of an inconclusive disagreement between Tim and I. I think it does, but I would also say that a knife does and so does a float. Tim and I are in agreement that rasps do not cut kerfs. Tim says kerfs are related to set, and a beveled veneer blade, or knife for that matter doesn't have set so the idea of a kerf becomes irrelevant. Of course it could be argued that a beveled blade has single sided negative set. Put that in your saw spectra chart and smoke it! |
Do you not have access to a block plane at your place of employ? That is the tool of choice (along with a chute with thin rails for the plane to ride on) for reducing the thickness of a strip of veneer.
I think you are correct about the plane technique, however I tried several versions of that type of set up and had a lot of trouble with it. Whether this was because of flawed technique or a peculiarity in the grain is unclear, but I just couldn't get it to work.
www.flickr.com/photos/chevy_chase_hughtos/6281736465/in/photostream
I'd love to see a pic of yours completed.
Sean- super stoked on your designs, and the SAMURAI. If you were to use reclaimed materials for the veneer it would be a sweet re up of the Gee's Bend quilting style.
Re: pics of finished veneer/project/humidor
Full report/blog/disaster coming soon...